Ekos is a comprehensive brewery management system that makes identifying batch issues and taking action straightforward.
one, cloud-based system of record
Finding out a batch you crafted is contaminated can halt all operations and have a significant impact on your reputation and business. It’s all hands on deck, but if you don’t know where to start or how to determine what happened, how do you take action before it has a chance to cause irreparable damage?
With Ekos lot tracking, you build a strong foundation for enhancing quality control and aligning with industry best practices. From production to distribution, lot tracking gives you the ability to preserve the chain of custody. Plus, if you’re maintaining any certifications or trying to ensure compliance with traceability laws, lot tracking reduces the need for having records outside of Ekos.
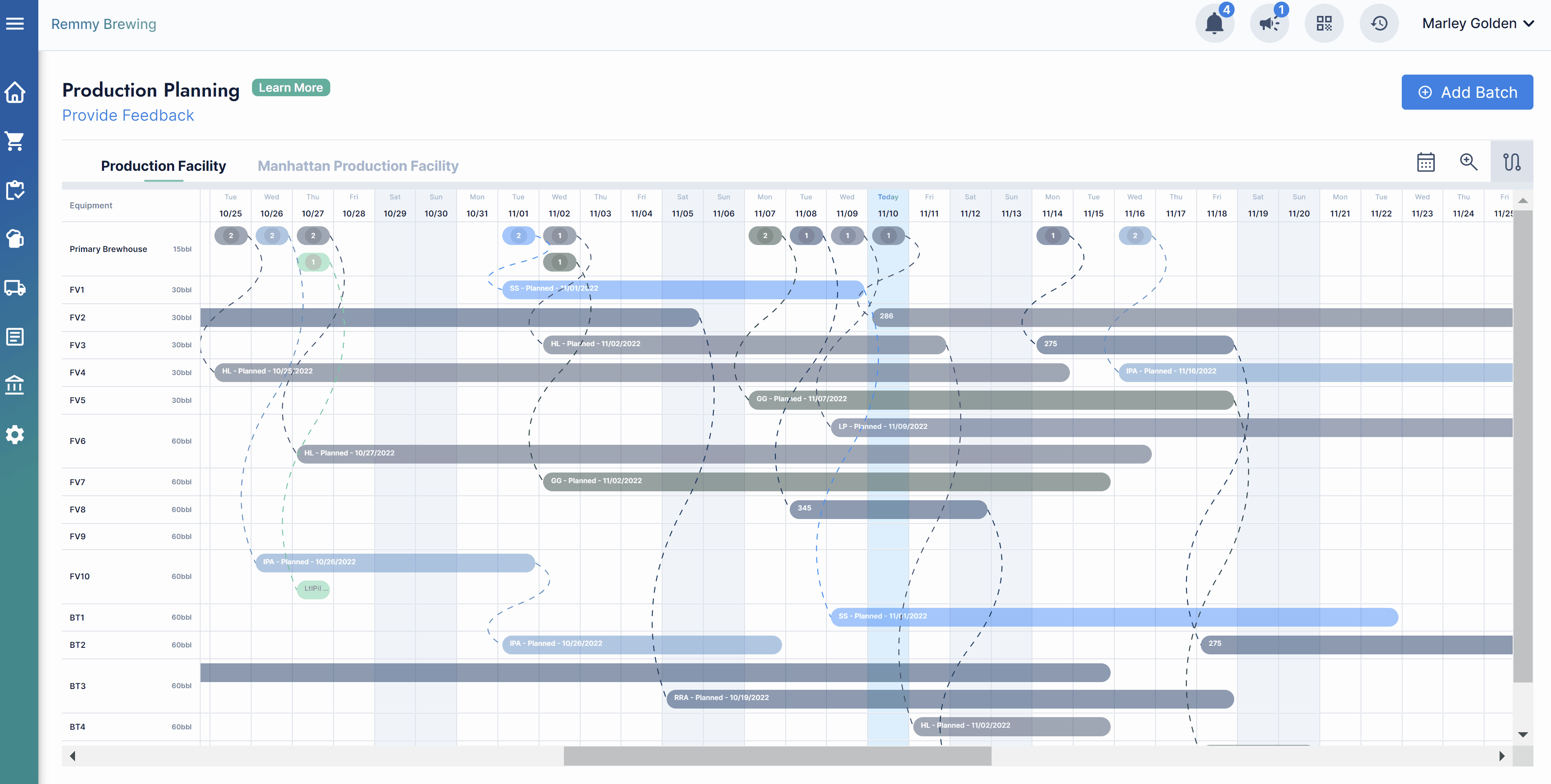
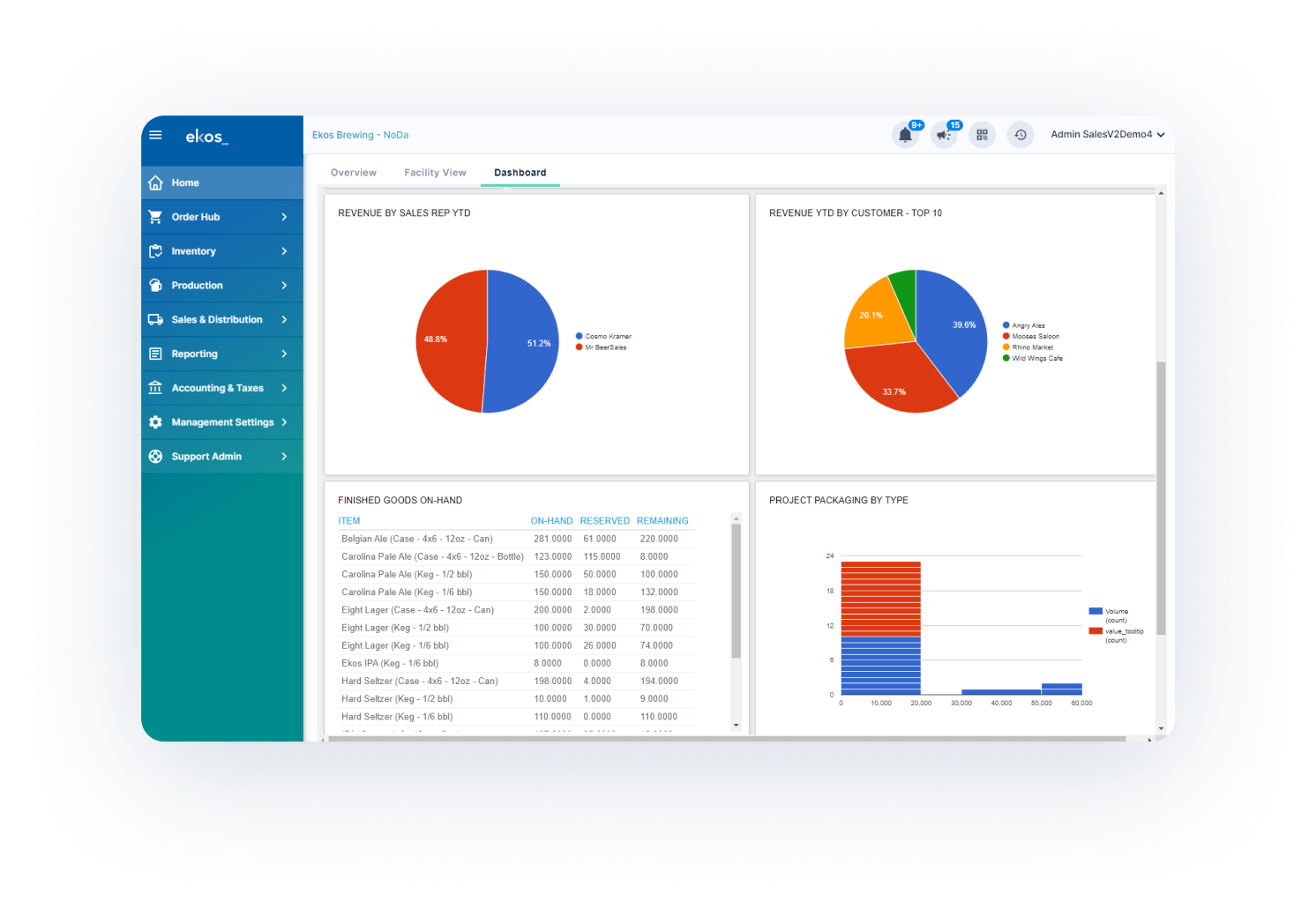
lot tracking for less stress
Lot tracking is a recommended best practice by both government and industry authorities to mitigate risk in case of a recall. Should you ever have an issue with a batch, lot tracking in Ekos will show you exactly where something went wrong. This functionality adds an extra layer of quality assurance to help guarantee consistency across batches, including barrel aging programs.
Ekos houses all of your production data in one place, from raw ingredients to fermentation dates and packaging, making it easier to identify the source of issues and quickly take action. With accurate data in hand, you can proactively shore up processes to minimize the risk of it happening again.
key capabilities
- Keep track of raw ingredients and packaging materials by lot code
- Choose the lot picking method that works best for your business (FIFO, LIFO, or FEFO)
- Use lot codes to determine which finished goods should be shipped to customers first
- Maintain certifications by leveraging data from Ekos
key benefits
- Group data by packaging run to more clearly organize batches
- Easily print labels to help identify which lots are associated with packaged goods
- In case of recall, quickly find the affected batches and where/when they were distributed
- Ensure compliance with traceability laws
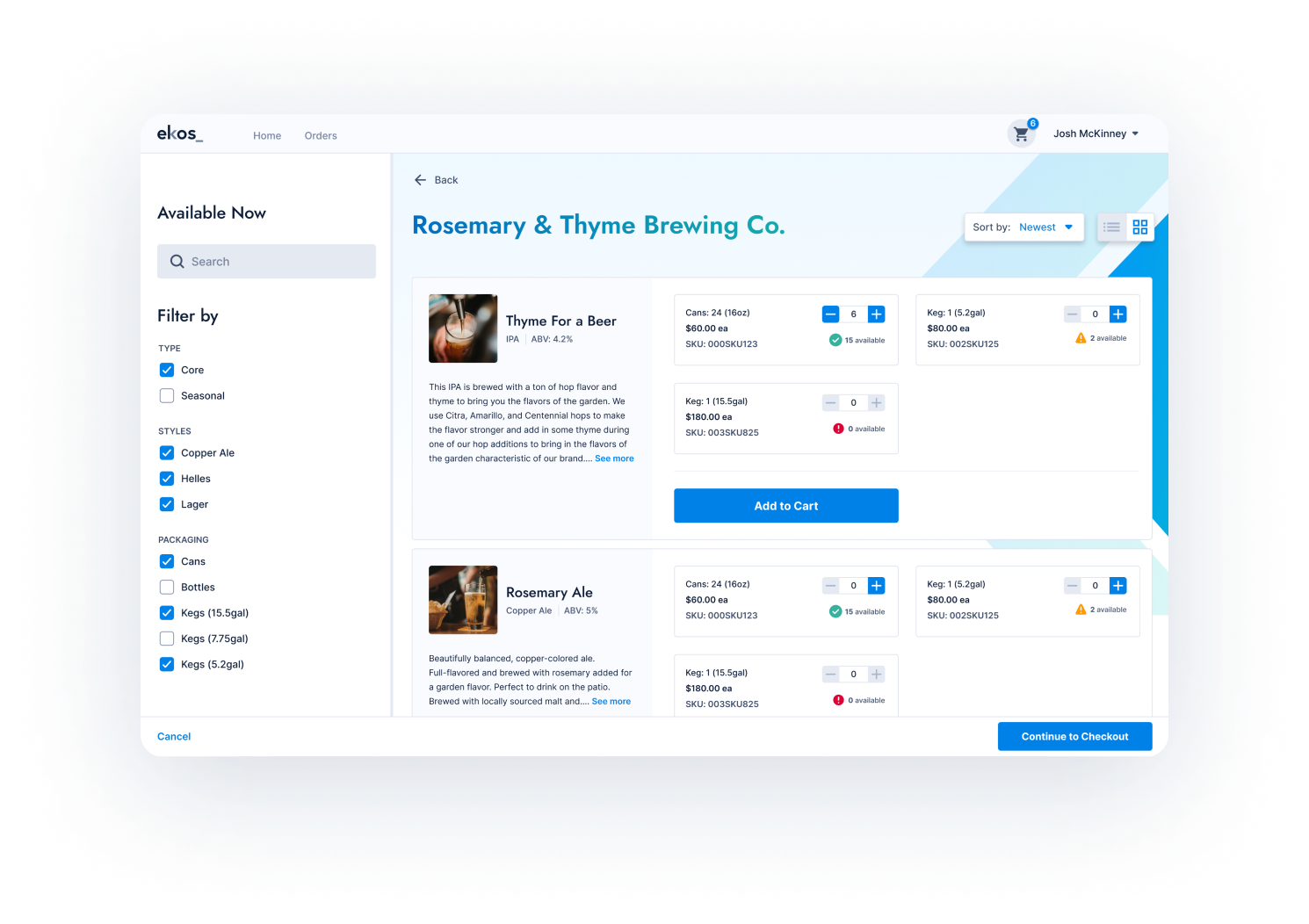
lot tracking is just the beginning
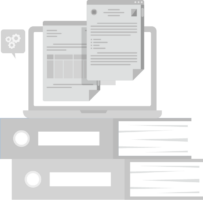
Ekos was built to help beverage makers run their businesses better, save time, and gain the insights they need to make smarter business decisions. Our all-in-one business management software is so comprehensive and automated, it can turn the nightmare of contamination into a manageable risk.
With all of your employees entering information into Ekos, you spend less time digging into separate systems or making calls when an issue with a batch arises. Each step of the crafting process is documented down to the raw ingredient level, so you can build stronger quality control and speed crisis control for a healthier product and business.
what our craft beverage makers are saying
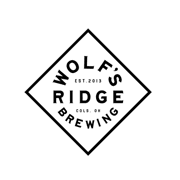
“Asset tracking is everything. Knowing where our kegs are allows us to provide reliable customer service to our accounts. I’m not sure it would be possible to stay on top of our 3,000+ kegs without Ekos.”
– Adam Hickernell, head of distribution, Wolf’s Ridge Brewing
Success Story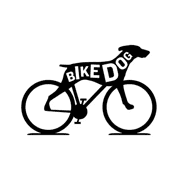
“We use Ekos to manage our brewery, including tracking 600-700 kegs to identify when they go missing. It’s helped us manage our self-distribution operation seamlessly and keep track of our growing fleet of kegs.”
– Sage Smith, co-owner of Bike Dog Brewing
Success Story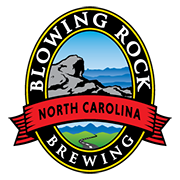